原子力システム 研究開発事業 成果報告会資料集
金属燃料の溶融塩電解精製における陰極・陽極の処理に関する研究開発
(研究代表者)飯塚政利 原子力技術研究所次世代サイクル領域 主任研究員
(再委託先)国立大学法人 豊橋技術科学大学
1.研究開発の背景とねらい
地球環境の変化やエネルギー消費の拡大に対応するため、原子力エネルギーを平和的かつ安全に利用することの重要性が増しており、これに伴って安全性、経済性、核拡散抵抗性に優れた核燃料サイクル技術が求められている。これらの要求を満足する技術の一つとして、金属燃料高速炉と乾式再処理プロセスからなる金属燃料サイクル技術(図1)が提案されている[1]。乾式再処理フローシートの中心となる溶融塩電解精製では、せん断された使用済金属燃料を受け取り、ここから核分裂生成元素(以下FP)を取り除き、燃料物質を回収する(図2)。陽極では、各種金属元素の塩化物生成自由エネルギー変化の差を利用して専らZr よりも塩化物生成傾向の強い元素を溶解する。U は金属製固体陰極の表面に回収し、残るアクチニド元素については、液体Cd 中における活量係数が低く還元されやすい性質を利用し、液体Cd 陰極にU と共に回収する。U は使用済金属燃料中の70〜90wt%を占める最大構成要素であることから、固体陰極におけるU 回収速度は、電解精製技術の工学的成立性、ひいては乾式再処理プロセスの経済的成立性を見通す上で非常に重要な性能となる。このためU 回収速度向上を図った装置開発と試験が行われ、直径役30cmの電極アセンブリを用いた工学規模試験において、789g-U/h という実用化に十分な速度が達成された[2]。しかし、電解精製を使用済燃料からアクチニドを回収してリサイクル燃料原料とし、かつ核分裂生成物を分離廃棄する工程として捉えると、次のような課題が残っている。
(1)陽極残留物処理技術の開発
- 電解精製終了後も陽極残留物中に少量残るアクチニド回収プロセスの開発
- SUS 被覆管、Zr、貴金属FP からなる陽極残留物を主体とする金属廃棄物処理プロセスの開発
(2)陰極回収物処理技術の開発
- Zr が混入することにより融点が上昇したU 回収物のインゴット化(付着塩蒸留除去、U-Zr 溶融固化)
- 高温の溶融U-Zr 合金/塩化物との両立性をもつ蒸留るつぼ材料の開発、および実用機器設計
そこで本事業では、実際にU 電解試験で生じた陽極残留物と陰極回収物、および模擬混合物を用いた高温蒸留試験などを通じてこれらの技術開発を行う。さらに、電解精製工程、陽極残留物/陰極回収物処理工程における技術的な到達度や性能を整合させつつ、U 回収率と回収速度を高いレベルで両立するための運転条件を定め、これを基に乾式再処理プロセスにおけるマスバランス、回収率などの性能を評価する。
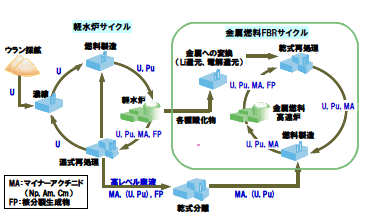
図1 金属燃料サイクルの概念
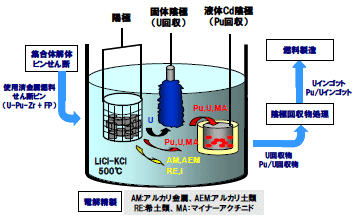
図2 電解精製工程の概念図
2.研究開発成果
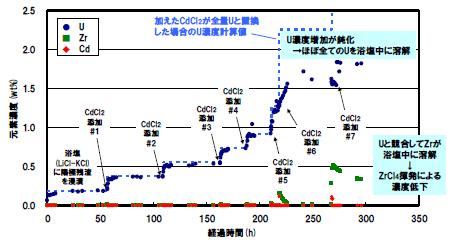
2.1 陽極残留物の処理技術開発
2.1.1 U-Zr 陽極溶解残留物からのU 溶解除去試験
電解精製工程において、陽極溶解後の残留物中に残るアクチニドを乾式再処理プロセスに戻すため、過去にU-Zr 合金を用いて実施した電解精製試験[3]で発生した陽極溶解残留物に酸化剤を加えて未溶解U を化学的に溶解する試験を実施し、陽極残留物処理方法としての適用性を調べた。
陽極溶解残留物約500g に、酸化剤としてCdCl2 を添加し、未溶解Uを溶融塩中に溶解させる試験を2回実施した。この陽極残留物は、SUS 被覆したφ5.8mm のU-Zr 合金を長さ約5mm にせん断したピンから大部分のU が溶解したものであり、模擬FP 元素は含んでいない。
1 回目の試験では、U/Zr の溶解反応の競合やU 溶解速度などについて基本的な知見・データを得るために、CdCl2 を数ステップに分けて行い、その後の溶融塩中元素濃度変化を長時間にわたってモニターした。電解精製試験終了時に評価された陽極残留物中の残留U 重量比(2.84%)から、使用した陽極残留物中に含まれるU 量を予測し、このU 量に等しい化学当量のCdCl2 を4 等分割して加えることにより、残留U を酸化・溶解させた。実際にはこの4 回ではU が全量溶解していないと判断されたため、さらに3 回追加し、最終的には当初予定量の約5.7 倍のCdCl2 を添加した。この試験における溶融塩中U/Zr/Cd 濃度変化を図3 に示す。酸化反応におけるマスバランスは概ね良好であったが、試験後半に陽極残留物中のU が涸渇し、引き続いてZrCl4 が生成して揮発するにつれて悪化した。試験終了後に採取した陽極残留物のICP-AES/WDS 分析結果から、それぞれのピン中のU 残留量は2〜3mg 程度にまで減少していることがわかった。
2 回目の試験では、1 回目の試験結果をもとに陽極残留物中に含まれる初期U 量を重量比6.95%と評価し、これに近い化学当量のCdCl2 を短時間に加えることにより処理時間の短縮を図った。Uの後に溶解するZr の溶融塩中濃度変化から、約2 日間でU 溶解反応が完了することが確認されたため、処理速度の面からは乾式再処理プロセスへの適用性が十分にあると評価した。
2 回の試験で得られた陽極残留物の分析結果から、電解精製とCdCl2 添加による溶解除去とを通じたU 残留率は0.1〜0.3%程度であることがわかった。乾式再処理プロセス全体における目標回収率がU については99.5%、超ウラン元素については99.9%であることを考慮すると、上記の残留率は電解精製工程のみにおけるロスとしてやや大きく、他の工程において生じるロスを想定すれば、さらに低減させることが望ましい。ただし、ここで残留物としてカウントしているU には付着・浸込塩浴中のUCl3 も含まれていることから、CdCl2 添加による溶解除去を含めた電解精製工程におけるU 回収率がプロセス検討上の要件を満たすかどうかの判断を現段階で下すのは困難であり、今後の研究開発の中で、高温蒸留により塩化物を除去した後に再度残留U 量を定量することが必要である。
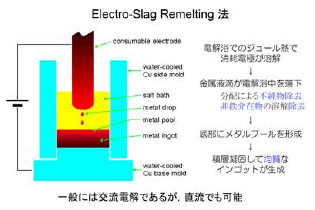
図4 ESR 法の概念
2.1.2 陽極残留物からのアクチニド除去工程への高温金属再溶解法の適用性検討
陽極残留物からのアクチニド除去工程に対する、鉄鋼等の再溶解法の1つであるエレクトロスラグ再溶解法[4](以下ESR 法、概念を図4 に示す)の適用可能性を調べるために、模擬物質を用いていくつかの基礎的な試験を実施した。
約420℃の溶融塩化物浴中で亜鉛を用いた再溶解実験では、電流を印加した際の亜鉛液滴の挙動変化を目視観察した。その結果、直流電解時に液滴の形成と滴下が促進される条件があることが明らかになった。一方交流電解時には特に低周波数側で形成される液滴が振動し、滴下に至る現象が見られた。また、マグネシウム含有液体亜鉛金属の電解試験では、亜鉛液滴を直流・陽分極させた場合に最も亜鉛からのマグネシウム除去効果が得られたことから、陽極残留物の主体であるステンレス鋼に含まれる化学的により活性な不純物に対してもDC-ESR 法で直流・陽分極させることにより効果的な除去が行える可能性が高いと考えられた。
高周波誘導炉を用いたSUS 鋼と溶融スラグ間の元素分配測定試験では、スラグ中への酸化材添加が不純物除去におよぼす影響を調べた。模擬不純物として珪素を加えたステンレス鋼を、酸化鉄を含む酸化カルシウム−酸化アルミニウムスラグと接触させた場合に、激しい反応が起こることを目視により確認したが、珪素含有量は大きく変化しなかった。これは、ステンレス鋼中に多量に含まれるクロムの酸化が珪素に優先したためであると考えられ、クロム酸化物を酸化剤として用いる方が好ましいことがわかった。
直流ESR 装置を用いた溶解予備試験では高珪素鋼とSUS 鋼を用い、これらの溶解可能性を確認すると共に必要な条件を把握した。その結果、過度の電流印加は形成されるインゴット断面に空隙を生じるなどの悪影響を与えるため、1kA 程度の電流が適当であることがわかった。
直流電流と交流電流を用いた場合を比較検討するために交流ESR 電源の詳細設計を実施した上で導入した。また、高珪素鋼やステンレス鋼の溶解に必要な条件を調べ、今後の検討課題を以下のように明らかにした。
- 良好な高珪素鋼インゴットを得るために必要な条件(槽電流、槽電圧、スラグ組成、電極間距離)の把握
- 珪素除去効果に与える槽電流、槽電圧、スラグ組成、添加元素の影響把握
- ステンレス鋼の溶解が可能な槽電流,槽電圧範囲の特定
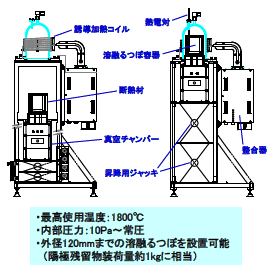
図5 金属廃棄物溶融固化試験装置
2.1.3 アクチニド除去後の陽極残留物の溶融固化試験
アクチニド溶解除去及び蒸留工程を経た陽極溶解後残留物を模擬したSUS(被覆管)/Zr/貴金属FP 混合物を対象とした溶融固化試験を実施するために、金属廃棄物溶融固化試験装置を設計・製作した(図5)。
本試験装置の真空容器上部は石英製ベルジャー、下部真空チャンバー・フランジ部はSUS304 製であり、これらを連結した状態で内容物の酸化を防止するために装置内雰囲気をAr に置換・維持し、内部圧力はロータリー式真空ポンプを用いて10Pa まで減圧できる構造とした。石英ベルジャー内にはカーボン製の溶融固化るつぼ容器を収納する。高融点のステンレスおよびZr をさまざまな混合比で溶融させるために、るつぼ容器は高周波誘導コイルにより最高1800℃まで加熱可能である。真空チャンバーは、今後装置下部に揮発物凝縮部を付加することにより工学規模蒸留試験装置への改造が可能となるように設けたものである。
本装置を実験室内に設置した後、基本性能試験を実施した。その結果、装置内部圧力を十分低く(10Pa 程度)保持できること、1 時間以内にるつぼ容器を最高使用温度1800℃にまで加熱可能であること、加熱コイルや真空バウンダリーに加熱による不具合が生じないことがわかり、本装置が金属廃棄物溶融固化試験に適した条件を満たすことが確認できた。
2.2 陰極析出物の処理技術開発
2.2.1 U-Zr 陰極回収物の高温蒸留処理試験
過去の電解精製試験で得られたU-Zr 陰極回収物、あるいは前述の酸化剤添加により残留U を溶解除去した後の陽極残留物を対象とした高温蒸留処理試験を行うために、U-Zr 陰極回収物蒸留試験装置を設計・製作した(図6)。
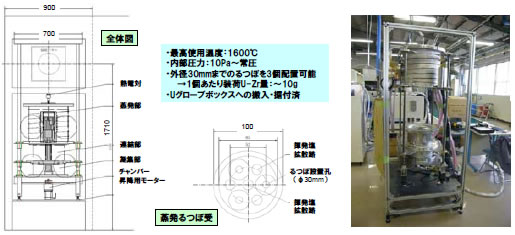
図6 U-Zr 陰極回収物蒸留試験装置
本装置は、試料を加熱する蒸発部、揮発した塩化物を拡散移送する連結部、揮発塩化物を捕集する凝集部から構成されており、これらを連結した状態で、ロータリー式真空ポンプを用いて10Pa程度まで減圧可能である。高融点のZr 含有陰極回収物を均一にインゴット化するために、蒸発部は高周波誘導コイルにより最高1600℃まで加熱可能である。蒸発物には多種の陰極回収物・るつぼ材料を用いた試験が効率的に実施できるよう、直径30mm までのるつぼを3 個同時に配置できる構造とした。連結部は揮発塩化物が凝固して閉塞を起こさないように抵抗加熱ヒータにより700℃まで加熱できる。凝縮部には、揮発塩化物を凝縮する冷却銅ブロックと、カーボン製るつぼを設置した。試験装置の昇降には、蒸発部用2 機、連結部用2 機のステップモーターを設置した。
本装置を既存U グローブボックス内に設置した後、基本性能試験を実施した。その結果、約1 時間で蒸発部が最高使用温度1600℃に到達すること、連結部を塩化物凝固による閉塞を防止できる温度(600〜700℃)に保持できること、凝集部を塩化物凝固・回収に適した温度(約200℃)に保持できること、塩化物揮発が促進されるよう装置内部圧力が十分低く(20Pa 程度)保たれることがわかり、高温蒸留試験に適した条件を満たすことが確認できた。
3.今後の展望
(1)陽極残留物の処理技術開発
- U 溶解除去試験を経た陽極残留物に浸込・付着するU を含んだ塩浴を除去するために、高温蒸留による揮発分離試験を実施し、最終的なU 残留率を評価する。
- ESR 法による不純物除去精製効果について、電流印加方法(直流/交流)や電解浴への酸化剤の添加などの溶解条件が及ぼす影響の観点から評価する。また、SUS 鋼のESR 実験を行い、良好な溶解が行える溶解条件の範囲を明らかにする。
- SUS、Zr、貴金属からなる模擬陽極溶解残留物の溶融固化試験を行う。組成、溶融温度などをパラメータとし、得られる固化体の微細構造、均質性、浸出挙動を調べ、廃棄物固化形態としての適用性を確認する。また各種セラミックスのるつぼ材料としての両立性についても評価する。
(2)陰極析出物の処理技術開発
- 電解精製試験で得られたU-Zr 陰極回収を対象とした蒸留試験を実施し、付着塩浴を除去すると共に、陰極析出物中のU-Zr をインゴットとして回収する。また、るつぼ材料として複数のセラミック及び複合素材を使用し、溶融U-Zr 合金/塩化物との両立性を評価する。
- 金属廃棄物溶融固化試験装置の高周波誘導加熱部を改造することにより、電解精製工程で得られる固体陰極回収物に換算して1kg-U 程度規模の蒸留装置を設計・製作する。この蒸留装置を用いた試験により、固体陰極回収物および陽極溶解残留物からの付着塩除去とインゴット化に適した設計・運転条件を把握する。
(3)陰極析出物/陽極残留物処理を含めた乾式再処理プロセスの構築
- 本事業における試験結果をもとに、陽極残留物処理で生じるアクチニドを含む塩化物、および陰極析出物処理で生じる揮発塩化物について発生量と組成・性状を評価した上で、乾式再処理全体におけるアクチニド回収率を高く保持するために、これらの副生成物を効率的に電解精製工程にリサイクルするためのプロセス設計を実施する。
4.参考文献
[1] T. Inoue, T. Yokoo and T. Nishimura, “Assessment of advanced technologies for the future nuclear fuel cycle,” Proc. Int. Conf. on Future Nuclear Systems (Global’99), Jackson Hole, WY, Aug. 29-Spt. 3, 1999 (1999).
[2] 文部科学省委託研究「金属燃料の乾式再処理プロセスの合理化に関する技術開発」、平成18年度成果報告書
[3] 同上 平成17 年度成果報告書
[4] 成田貴一ほか;「エレクトロスラグ再溶解法の物理化学と技術的諸問題−特殊精錬部会最終報告書−」, 1979.