原子力システム 研究開発事業 成果報告会資料集
レーザー加工技術の組み合わせによるFBR熱交換器伝熱管内壁検査技術の高度化に関する技術開発
(研究代表者)西村昭彦 量子ビーム応用研究部門 研究主幹
1.研究開発の背景とねらい
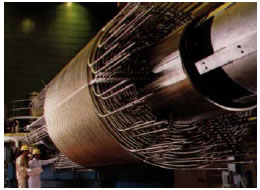
写真1 「もんじゅ」熱交換器
本事業では次世代ナトリウム冷却型FBRにおける蒸気発生器のための検査補修技術の高度化のために、内壁面に生じる微小欠陥等を早期発見し、その場での補修を可能とする新プローブの開発を目的とする。
本課題の背景として、FBRに関するものとしては、熱交換器内で共存するナトリウムと水の化学反応に対する長年の危惧がある。一方でレーザー加工技術に関するものとしては、超短パルスレーザー加工の著しい進展がある。本手法は透明材料の内部加工において有効な手法であり、光導波路などの光電子デバイス開発への応用が積極的に展開されている。一方、原子力エネルギー分野での利用としては、2002年に国内のBWRで生じたシュラウド応力腐食割れ問題を契機として、超短パルスレーザーによる加工硬化層の蒸発除去を新たな応力腐食割れ対策技術として発案した[1]。その後も原子力材料への適用拡大に傾注した結果、超短パルスレーザー蒸発をミクロからマクロにかけてスケールの異なる新たな応用が可能となった。マクロ応用例としてはシュラウドを対象とした超短パルスレーザー蒸発の大面積化を実施した。2005年には1 cm2の応力除去に成功、続いて2006年には1x10 cm2の応力除去に成功した。
これにより、新たな応用分野としてFBRの熱交換器伝熱管の補修技術の開発が可能となった。写真1にもんじゅ熱交換器伝熱管を示す。現在のFBR原型炉であるもんじゅの熱交換器は蒸発器と過熱器を組み合わせた構造であり、蒸発器の伝熱管内には高温水と蒸気が混相流として流れ、外側を液体ナトリウムが流れる。これまでは渦電流探傷(ECT)による検査により伝熱管に欠陥が発見された場合、伝熱管を施栓により塞ぐのが対処の基本である。しかしながら施栓の割合が高くなると有効伝熱面積の減少となり、結局は熱交換器の寿命を縮めることとなる。現在、ECTの検出性能の向上とともに伝熱管内壁の微細な欠陥の発見が可能となりつつあり、発見した微細な欠陥を補修することで施栓を回避することが望まれる。本プロジェクトでは、伝熱管を検査だけでなく欠陥の発見に併せてその場での補修を試みる新型プローブを開発する。これに必要な経験がITER核融合ブランケットの枝管をレーザー溶接・切断するロボット装置として、1999年に複合光ファイバを用いたレーザー熱加工による補修である。ITERプロジェクトでの開発終了後、この複合光ファイバは光ファイバ内視鏡とレーザーメスの融合技術として積極的な医療応用が進められている[2]。
以上のように本課題には、もんじゅの後継にあたる次世代FBRの熱交換器伝熱管の検査補修技術の推進として、レーザー技術、原子力、医療という離れた分野間の連携によって新技術のブレイクスルーがねらいとして含まれている。
2.研究開発成果
2.1 概要
開発するシステムは、次世代FBR熱交換器の伝熱管を検査補修するための新型プローブシステムであり、ECT検査技術、複合型光ファイバ技術、レーザー熱加工および超短パルスレーザー加工技術を統合させ、従来の検査機能に補修・保全機能を備えている。
図1に新プローブの概要を示す。これまでに主要技術の整備は順調に進展し、実機製作に向けての問題点を明確に出来た。開発のコアとなる技術は、伝熱管内壁の映像を伝送する画像用光ファイバと欠陥部位のレーザー熱加工溶接による補修のためのエネルギー伝送用光ファイバを同軸構造に組み合わせた複合型光ファイバである。レーザーとしてはCO2レーザーやYAGレーザーに加えて小型高性能化が著しいイッテルビウムファイバレーザーガ有力である。複合型光ファイバの周りには照明用のライトガイドも設けられている。このファイバの先端には伝熱管の内壁の撮影と加工補修のためのレーザー加工ヘッドが接続する。レーザー加工ヘッド内には伝熱管内壁を360度スキャンし、レーザー照射位置を微調整するための小型ステッピングモーターが内蔵される。また、複合型光ファイバの反対側の端面では、画像とレーザー光の分離装置を設ける。さらにレーザー加工ヘッド直近には複合型光ファイバを抱え込む形でECT用マルチコイルセンサが取り付けられる。
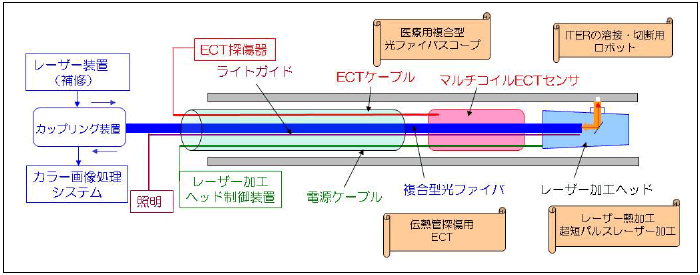
図1 新型プローブシステムの構成概要
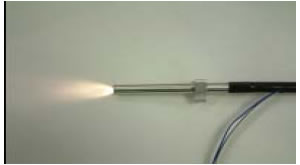
写真2 複合型光ファイバスコープ
2.2 複合型光ファイバスコープ
複合型光ファイバスコープは、熱加工用のための1kWレーザー光が伝送される。レーザー光を伝送する中心部分のコア直径は200μm、クラッド直径は220μmである。レーザー伝送部コア材質は純粋石英ガラスである。このレーザー光伝送部の周囲に画像伝送用ファイバが同軸上に取り囲む構造となっている。画素数は20,000画素とし、画像伝送部径φ0.8mmとした。この画像伝送部コア材質はGeドープ石英ガラスである。複合型光ファイバスコープの一端には石英ガラス製対物レンズを設けた。レンズ表面にはレーザー光の波長である1070nmのARコートを施した。
先端のレンズ周囲には照明用ファイバを一層配列した結果、外径約7mmとなった。写真2は複合型光ファイバスコープの先端のステンレス製スコープ部分である。スコープの先端からの光りは照明用ファイバからのものである。スコープの柔軟部分の可撓性は、最小曲げ半径45mmであり、挿入する熱交換器の伝熱管の屈曲部分にも充分対応できる。
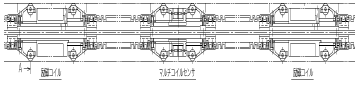
図2 ECTセンサユニット
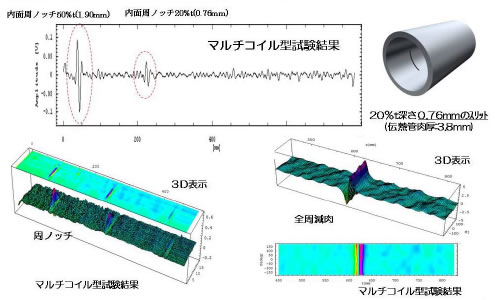
図3 マルチコイルからの出力結果
2.3 ECTセンサヘッド
渦電流探傷により微小な内壁欠陥を発見するのがECTセンサヘッドの役割である。マルチ型の検出コイルと2個の励磁コイルとを組み合わせたECT中空センサユニットを設計した。図2にそれぞれのコイルの配置を示す。長さ約50mm、外径約20mmのマルチ型検出コイルの両側に励磁コイルを配し、励磁コイルが伝熱管に誘導する渦電流により生じる磁場をマルチ型検出コイルで検出する。伝熱管内壁に欠陥がある場合、深さと形状を可視化できる。ECTセンサの中心軸には複合型光ファイバが通り、新プローブ組み立て時には複合型光ファイバと一体化させた。
今回製作したECTセンサヘッドの基本性能を示す。図3は伝熱管の内壁に20%と50%のノッチがある場合のマルチコイル型センサからの時間波形を示す。20%ノッチでも充分な強度の信号を得た。各コイル間の抵抗値の補正とコイルと伝熱管壁との距離の偏差を校正することで精度の良い画像化が可能となった。
これまでの試験により検出部にマルチ型コイルを用いることで内面局部減肉5%t(L5mm、W10mm)及び内面周方向ノッチ20%t(L10mm、W0.3mm)を検出できる見通しを得た。また、図3にはECT制御用ソフトウェアの開発により伝熱管内壁の微小欠陥を迅速且つ高精度で立体表示を行った結果を示す。さらに、複合型光ファイバスコープと中空センサユニットとの組み合わせを実施し、ケーブル複合化や減数のためのマルチプレクサが重要となること等、課題を抽出した。
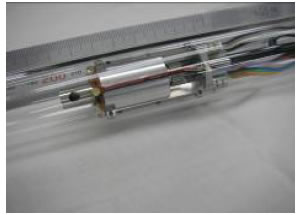
写真3 レーザー加工ヘッド(側面)
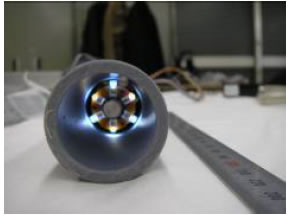
写真4 レーザー加工ヘッド(LED点灯)
2.4 レーザー加工ヘッド
複合型光ファイバスコープと組み合わせが可能なレーザー加工ヘッドを製作し、基本性能を確認した。レーザー加工ヘッドは、複合型光ファイバスコープの先端に接続し、1インチ程度の伝熱管内に挿入された状態で、周方向回転と軸方向移動への基本動作を行えるものとし、伝熱管内壁をレーザー光で集光照射できる構造とした。写真3にレーザー加工ヘッド示す。内径1インチの透明アクリルパイプにレーザー加工ヘッドを挿入し、動作確認を行った。レーザー加工ヘッドの可動スリーブ部分は軸方向に5mm、周方向に左右185度の動作が可能である。
伝熱管内壁の撮影映像の評価準備のため、複合型光ファイバスコープをレーザー加工ヘッドに挿入し、複合型光ファイバスコープのカップリング装置接続側にビデオカメラを接続し連続画像の撮影を試みた。アクリルパイプ内の文字撮影の結果、製作したレーザー加工ヘッドは動作状態において、複合型光ファイバスコープに連続画像を伝送できることを確認した。
写真4はパイプ内に挿入したレーザー加工ヘッドのLED照明を点灯させた状態である。このLEDは複合型光ファイバスコープの外周に設けたライトガイドの補助として用いる。また、レーザー加工ヘッドの専用制御用ソフトウェアの開発を行い、溶接熟練者による手動制御とその記録動作の実施を可能とした。また、高トルクな超音波モータの搭載やレーザー照射領域の伝熱流動解析の必要性などの開発課題を抽出した。
2.5 カップリング装置設計と製作
レーザー光と画像の分離・統合を行うためのカップリング装置の詳細設計を行い、その妥当性を確認した。カップリング装置は、最大出力1kWのレーザー光の使用を設計条件とし、内蔵するダイクロイックミラーにより、複合型光ファイバスコープからの映像と伝送するレーザー光の統合・分離が行える構造とした。レーザーは市販のイッテルビウムファイバレーザーを想定した。ダイクロイックミラーは反射率99%@1075nm、平均透過率90%@450〜800nmである。平成20年度は昨年度実施した詳細設計に基づいて本体の製作を行った。
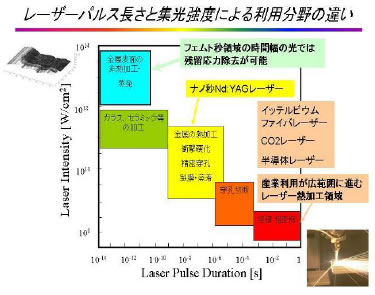
図4 レーザー加工応用分野の区分
2.6 模擬伝熱管補修試験準備
平成21年度には模擬伝熱管の補修試験を実施する。本年度は既設のレーザー装置を使用して、カップリング装置にレーザー光を安全に導入する試験を実施した。図4にレーザー加工の応用分野の分類を示す。既設のレーザーは図4の右下部分である熱加工領域に属するフラッシュランプ励起フリーランニングレーザーであり、半導体レーザーの大規模アレイの模擬レーザーである[4]。集光部分の直径はファイバコア径と同じ200μmとした。このレーザー照射条件は2.3×107 W/cm2であり、クロム鋼等の伝熱管材料に照射した場合、その表面は容易に溶融・蒸発する。実験の結果、合成石英窓板には損傷が見られないことを顕微鏡観察により確認した。
模擬伝熱管補修試験において、仮に最大出力1kWの市販イッテルビウムファイバレーザーを0.2mm直径に集光すると、集光強度は0.32×107 W/cm2となる。試験では2.3×107 W/cm2まで集光強度を上げても合成石英窓板には損傷が発生しなかったことから、充分な安全尤度がある。従って、ダスト等が抑制された環境下においては、複合型光ファイバスコープの端面やカップリング装置に損傷は発生しない。
3.今後の展望
図1に示した新プローブ完成に必要な各要素技術および模擬伝熱管補修試験についての概要について述べた。複合型光ファイバスコープは、10mの長尺と20,000画素数の試作に成功した。複合型光ファイバスコープとレーザー加工ヘッドは仮接続を行い、以降の実施内容の準備を開始した。ECT探傷については、もんじゅの3系統の熱交換器伝熱管検査の知見を反映し、従来型よりも高性能なマルチコイルセンサを採用した。平成20年度は、次世代FBR熱交換器として想定されている直管型の伝熱管の模擬補修試験を鑑み、カップリング装置の製作、ECT探傷器及びレーザー加工ヘッドの制御ソフトウェア及び各要素技術の統合を進めた。これより、新型プローブシステム全体を通じた改良点と補修方法に関する実効的な手順に関する知見を深める。
4.参考文献
[1] 西村昭彦、峰原英介、塚田隆、“ステンレス鋼表面の超短パルスレーザー光を用いた応力除去法”、特開2005-131704.
[2] 岡潔、エネルギーレビュー、7月号, 2007, pp.7-10.
[3] 科学技術振興機構報第394号, 平成19年4月19日, (http://www.jst.go.jp/pr/info/info394/index.html)
[4] A. Nishimura, et. al, “High energy flashlamp pumped Ti-sapphire laser for Yb:glass CPA”, SPIE - Proceedings, Vol.3265, 1998, pp. 234-241.